21 October, 2019Trade union representatives from six countries in South-East Asia gathered in Bangkok on 16 and 17 October to discuss how to best protect workers as industry undergoes rapid transformation due to digitalization and automation.
More than 30 participants from Cambodia, Indonesia, Malaysia, Philippines, Thailand and Vietnam, gathered for IndustriALL Global Union’s regional conference on Industry 4.0 and Sustainable Industrial Policy.
“Industry 4.0 is not just robots, not just artificial intelligence, not just big data, not just 3D printing – it’s all of these things,” said Brian Kohler, IndustriALL’s director for health, safety and sustainability. “There are great and rapid changes coming to the economy, driven by Industry 4.0, efforts to address climate change, and other forces. We want decent work, quality work and work that will sustain our families and our communities into the future.”
Industry 4.0 is fast invading South-East Asia, especially in the ICT and auto industry, said IndustriALL’s ICT, electric and electronics director, Kan Matsusaki:
“We don’t have any time to lose. We must influence governments and key employers now.” He said Taiwanese iPhone manufacturer, Foxconn, has shed around half a million jobs in the last five years, as it switches from workers to robots on production lines.
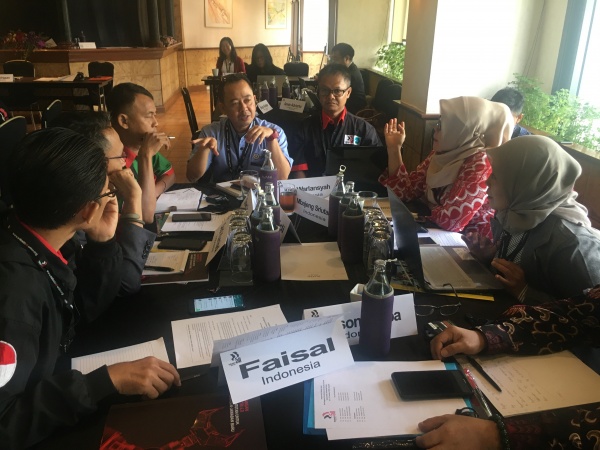
Unions discuss strategies for sustainable industrial policy.
Unions in the Philippines cited preservation of employment as the major challenge. They have successfully sustained jobs by lobbying to protect local car industries and campaigning against the massive importation of second-hand cars.
In Vietnam, unions see Industry 4.0 as an opportunity to attract more investment in the country and are determined to adapt to and adopt new technologies.
But several participants expressed concern that neither they, the employers, nor the government are prepared for the future.
“The Fourth Industrial Revolution and electric cars are going to be a real problem for us. We are worried many factories will close. We are making automotive parts for traditional combustion engines, not electric vehicles,” said Dedi Kurniadi from the Indonesian union, FSPMI.
In Thailand, government legislation compelling companies over a certain size to provide training and reskilling for employees, is not well implemented and trade unions have no say in the type of training on offer. Similarly, while unions have been able to push through 14 weeks maternity cover, this does not apply to precarious workers, who are often let go when they get pregnant.
"Industry 4.0 is affecting women worst – if jobs are cut, women will be let go before men," said Mbajeng Sriutami from FSPKEP in Indonesia.
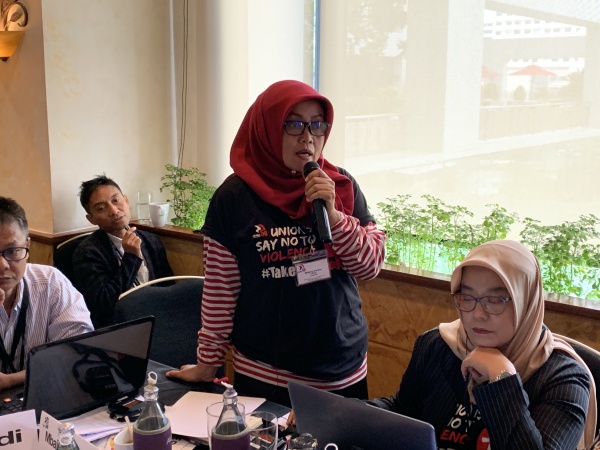
Mbajeng Sriutami from FSPKEP in Indonesia
In Malaysia, automation and digitalization has been slow to take off due to slow internet speeds and an abundance of cheap, migrant labour making it, for the moment, more expensive to use robots than people. Approximately 35 per cent of the country’s manufacturing workforce are migrants, said Mohd Saad, from EIEU.
IndustriALL’s regional secretary, Annie Adviento, said:
“We need unity among unions on the issue of Industry 4.0 and sustainable industrial policy. We must work together. Our counterparts in the employers and the government are very organized and they have a lot of resources. But unions have resources too and we must use them to get the best deal for workers.”
Participants agreed to produce an action plan to better engage with national governments on sustainable industrial policy, and also look at ways of engaging with NGOs and civil society movements with interest in the area.